Shark Solutions
Shark Solutions can extract new raw materials from broken windshields. The technology has required many years of development due to the exceptionally strong adhesive.
Sustainable Development Goals at play
• SDG 12: Responsible consumption and production
• Target 12.5: By 2030, substantially reduce waste generation through prevention, reduction, recycling and reuse
• SDG 9: Industry, Innovation and Infrastructure
• Target 9.4: By 2030, upgrade infrastructure and retrofit industries to make them sustainable, with increased resource-use efficiency and greater adoption of clean and environmentally sound technologies and industrial processes, with all countries taking action in accordance with their respective capabilities
Recycling car windshields or sending them directly to landfill? It may sound like an easy choice. Unfortunately it is anything but. Car windshields are not only made of glass but also of an extremely strong polyvinyl butyral (PVB) adhesive that holds the glass together should it break at high speed. In 2005, a team of ambitious entrepreneurs and researchers decided to try to separate the two components. Seven years later, they had cracked the code, Shark Solutions CEO, Jens Holmegaard explains:
‘Shark Solutions arose from the idea of generating raw materials from old car windshields and laminated glass, also known as safety glass. The challenge lies in the fact that these types of glass products are held together by an extremely strong adhesive, typically a 0.8 mm thick and completely transparent film. Consequently, it has taken us many years to figure out how to separate these two components. In 2013, we finally had a breakthrough, and today we have a fully commercial product on an industrial scale.’
In addition to the head office in Roskilde, Denmark, Shark Solutions operates three factories. The main factory is located in Belgium, while the two others are located on each side of the US mainland, in Atlanta and Los Angeles respectively. The locations are based on the availability of windshields, Jens Holmegaard explains:
‘In Belgium, we are close to some of the largest glass recycling companies in the world – which is also the case in Georgia and California. We are fully aware however, that we need to go to Asia to get the global reach we want. Our reluctance so far can primarily be explained by the characteristics of business structures and logistics, which are very different from what we know. Throughout the SDG Accelerator programme however, we have uncovered the most significant issues that previously held us back. Once the right partnerships have been established, we are now ready to get things going.’
Besides the geographical focus, the management team of Shark Solutions has also spent time identifying alternative usages of the PVB from windshields. While the glass itself is easily sold in its recycled form, it is far more difficult to recycle the adhesive, which according to Jens Holmegaard has great potential:
‘Initially, we imagined the purified PVB to be reused in the production of new windshields or windows for buildings, but it has proved impossible to make it transparent enough. Consequently, we had to look for other recycling opportunities. A natural choice could be the carpet industry, which is already searching for non-toxic alternatives to the current adhesives. The same goes for the paint industry, where adhesives make up a key ingredient. In both places, the recycled PVB is a sustainable alternative and therefore areas where Shark Solutions can build a sound business.
It has been a long, tough fight to get there, but the carbon we save by reusing the PVB is quite impressive.’
According to Jens Holmegaard, working with the Sustainable Development Goals through the SDG Accelerator programme has been an exciting and rewarding process:
‘The programme definitely gave us a broader perspective on our own business, and made us realise the impact potential in our technology, the actual difference it can make for the planet. UNDP has also been exceptional at opening some of those doors that we couldn’t open ourselves. For us, that meant being introduced to an entire new network that is ready to assist us in expanding our business further onto the global markets.’
Hence, Jens Holmegaard is both excited and optimistic on behalf of his company:
‘We now have an overview of how to source broken car windshields in Asia, and are already talking to a number of partners in the distribution network. We principally want to reach out to very large distributors and logistics companies that already know how to handle waste. The next step is to finalise these various agreements. After that, we are ready to set up local production.’
This is how Shark Solutions contributes to the Sustainable Development Goals
- Shark Solutions generates sustainable raw materials from old car windshields and laminated glass, which previously would have been sent to landfills.
- It has taken many years of intensive development to be able to separate the glass from the extremely strong PVB adhesive that holds it together.
Facts about Shark Solutions
- Founded in 2005
- The world’s leading manufacturer of recycled PVB adhesive from car windshields and laminated glass
- Factories in Belgium and the United States
- Head office in Roskilde, Denmark
- Approximately 55 employees.
‘Shark Solutions arose from the idea of generating raw materials from old car windshields and laminated glass, also known as safety glass. The challenge lies in the fact that these types of glass products are held together by an extremely strong adhesive, typically a 0.8 mm thick and completely transparent film. Consequently, it has taken us many years to figure out how to separate these two components. In 2013, we finally had a breakthrough, and today we have a fully commercial product on an industrial scale.’
Jens Holmegaard, CEO, Shark Solutions
Contact
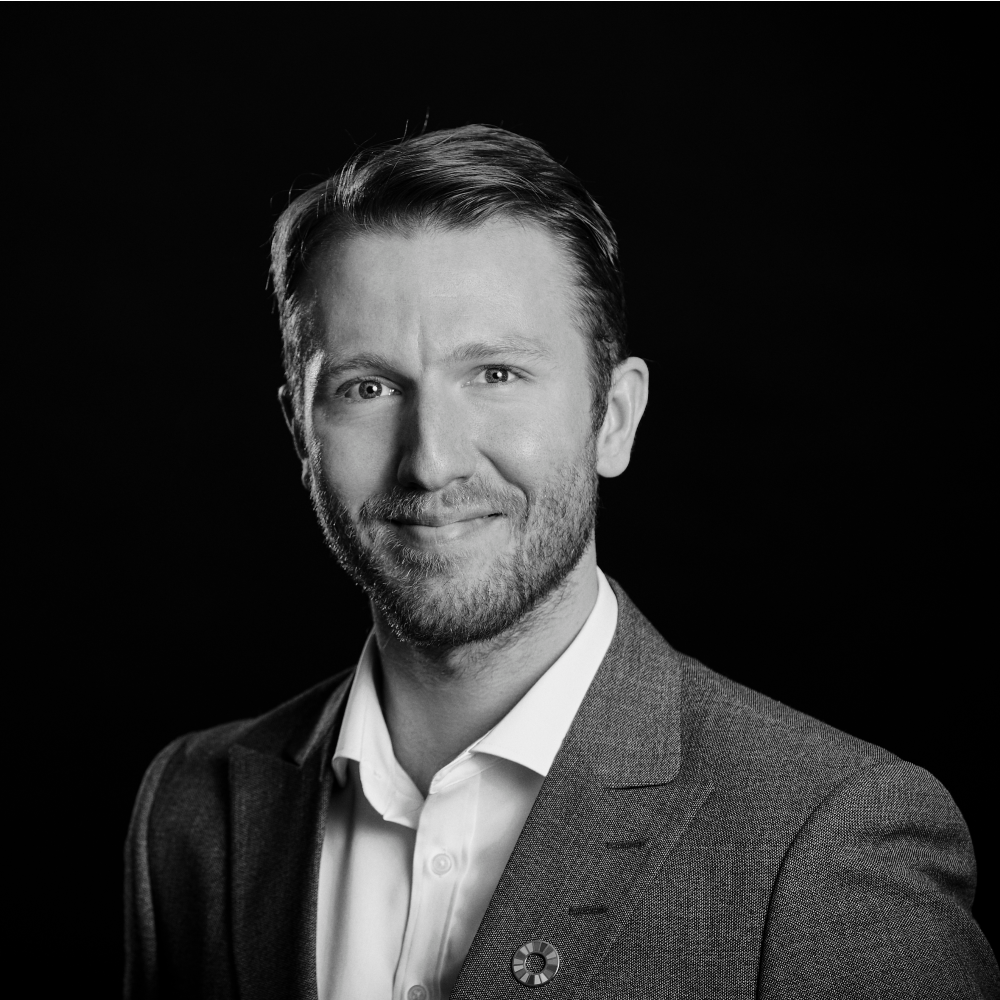