The prosthetic device specialists at ‘Bandagist Jan Nielsen’ in Copenhagen operate around 35 3D printers. They can print everything from artificial limbs to corsets that can straighten the back – with customisable options for the user.
3D printing of prostheses contributes to significant savings on carbon, water and material consumption. Further information can be found in the lifecycle report at www.bjn.dk/viden. The report has been created with assistance from Deloitte.
When prosthetist Jan Nielsen bought his first 3D printer eight years ago, many people shook their heads. What was he going to do with it? Wasn't it just for fun? And yes, to begin with it was mostly for fun, because you could print small houses or play with different designs. But it also became the start of the revolution that is now changing the entire prosthetic device profession where classic prostheses are now replaced with custom-designed 3D printed ones.
"Maybe I was just the nerdy boy who thought 3D printing was exciting, but from the beginning I saw a huge potential. I didn’t mind that some of my colleagues shook their heads. I knew that over time, we could realise great gains in terms of design, time and environmental impact,” says Jan Nielsen.
Today, 3D printing is an integral part of the company, and Bandagist Jan Nielsen currently prints about 70 % of its prostheses:
“There are many benefits of 3D printing. Instead of making a plaster cast of the patient’s leg, we can 3D scan it, which only takes a minute. And instead of going through a complex, manual process of modifying standard components by cutting, grinding and gluing, we can print a prosthesis that is tailored to the individual patient.”
An international network
Despite the many experiments with 3D printing, there is still a lot to learn, and the prosthetic device profession is very small, Jan Nielsen explains:
“Even though some prosthetists are experimenting with 3D printing, the technology is so new that we are still waiting for the big breakthrough in the international market. In other words, we have to develop the methods ourselves, and there is no instructional video to be found on YouTube. It is an exciting but demanding task.”
Jan Nielsen is grateful to be able to draw on an international network that mainly consists of American specialists:
“In the United States, there is a network of prosthetists that work with 3D printing, and this network is crucial if we are to move forward with the new technology. We are a very small industry, which fortunately consists of some passionate and sometimes crazy individuals. We work together to create the future, and we believe in a world full of opportunities.”
New solutions truly make a difference
One thing is the professional network, another is the users whose everyday lives are completely dependent on well-functioning prostheses. At the end of the day, our mission is to make their lives as easy as possible, says Jan Nielsen:
“The overriding advantage of 3D printing is that we can make a difference for people who are in a difficult situation due to illness or an accident. We recently had a patient with a femoral prosthesis that he could not take off by himself due to paralysis in one side of the body. By 3D printing a custom-designed prosthesis, he was able to put it on and take it off by himself. To outsiders it may be just a knob or a handle, but that knob or handle can sometimes make the difference between walking or sitting in a wheelchair.”
At the same time, 3D printing has also revolutionised the process of working with prostheses for children, says Jan Nielsen:
“Imagine a child who is born with a crooked back and needs a corset to straighten it. Previously, we had to cover the child in plaster before using a giant pair of scissors to cut it off. It created stressful situations with screaming children and desperate parents. All of that is avoided with 3D printing. Now we simply scan the child with a hand-held scanner, go to the workshop and print a corset that fits.”
The future of prostheses
According to Jan Nielsen, 3D printing carries a huge potential, even if not all prostheses can be manufactured in this way:
“When it comes to carbon fibre prostheses that can withstand both water and chemistry, we probably still have to rely on the classic manufacturing processes. But many other prostheses can be 3D printed. I would estimate that over half of all prostheses will be manufactured using 3D printing in the future. At the same time, 3D printing will be the obvious choice when testing prostheses for new amputees.”
Finally, it reduces the environmental impact, which was quantified during the AM Sustain programme. Calculations showed that 3D printed prostheses can reduce water consumption by 34 %, CO2 footprint by 51 % and material consumption by 70 % compared to traditional manufacturing, which are all significant gains according to Jan Nielsen:
“When grinding a prosthesis, we throw out at least half of the material. With 3D printing, there is practically no waste. This leads to significant environmental benefits, which we now know in detail thanks to the calculations we have carried out through the AM Sustain programme. This might not make a huge difference for the users, but for us as specialists the benefits are an important step on our journey towards designing better and more sustainable prostheses.”
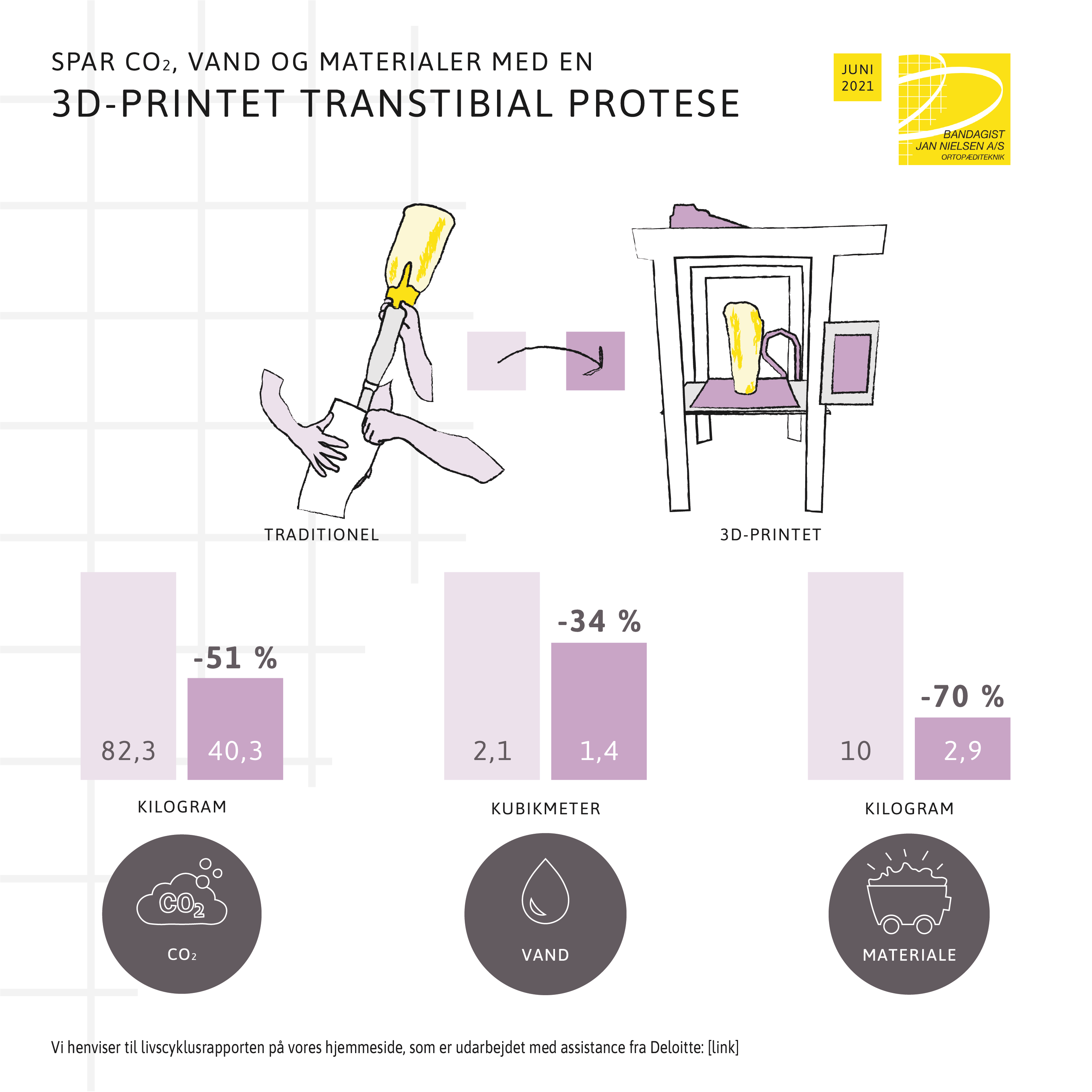
About Bandagist Jan Nielsen
- Bandagist Jan Nielsen A/S is one of Denmark’s leading suppliers of orthoses and prostheses.
- In addition to prosthetists, the company employs physiotherapists, specialised technicians, store staff and secretaries in Copenhagen.
- Bandagist Jan Nielsen A/S has its own sewing room and prosthesis workshop, including its own 3D printers for prostheses.
- The company was founded by Jan Nielsen.
About 3D-printed prostheses
- Today, 3D printing is used for a wide variety of prostheses such as leg prostheses, arm prostheses and finger prostheses.
- 3D technology can also be used for orthoses that support and correct body parts such as the head, back, neck or joints.
- Prosthesis users are just as different as everyone else, and no fitting processes are the same.
- With 3D printing, the prosthetist gets the maximum freedom of design to create a prosthesis that will make a difference for the individual user.
Contact
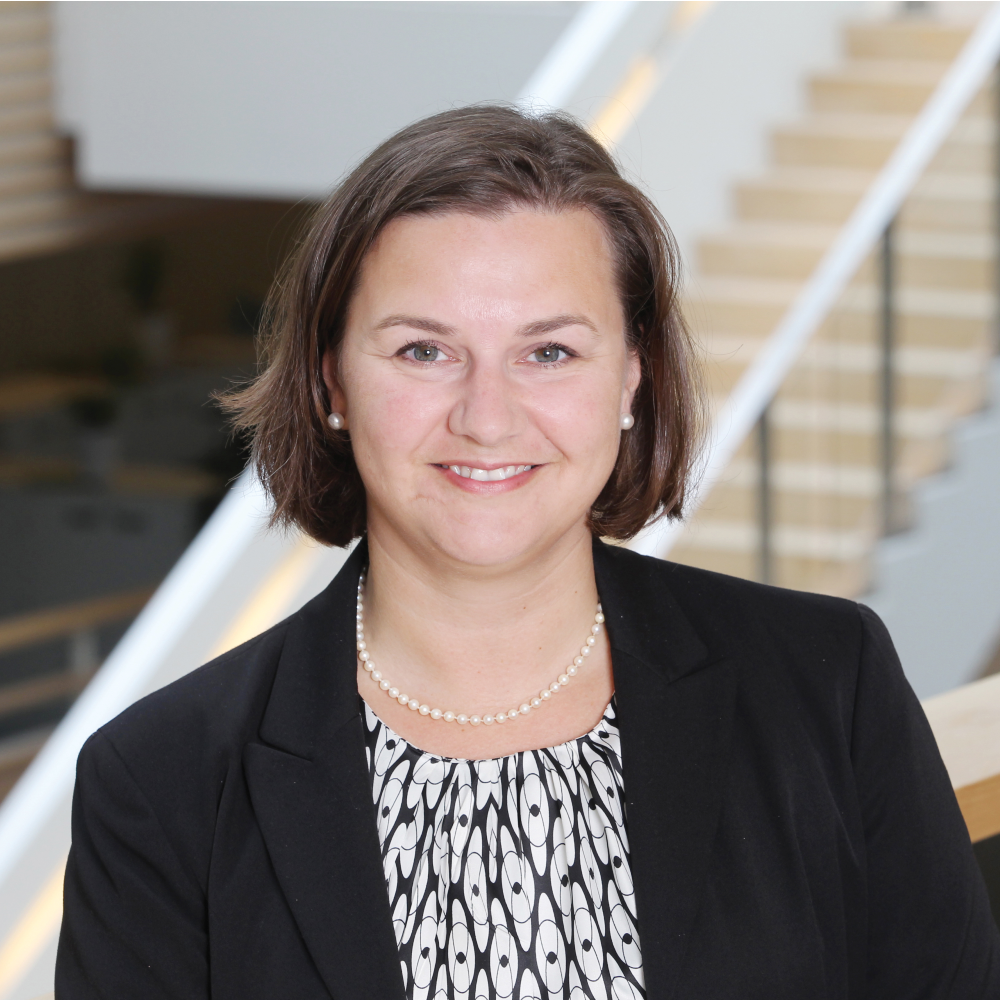
Helena Barton, Partner, Sustainability | ESG | Climate Risk
Helena Barton, Partner, Sustainability | ESG | Climate Risk
+45 30 93 68 13
Email Helena Barton, Partner, Sustainability | ESG | Climate Risk