The greenfield factory journey: Phase 3 has been saved
Perspectives
The greenfield factory journey: Phase 3
Startup: Virtual commissioning to product qualification
In part 3 of our four-part article series detailing Deloitte’s greenfield factory journey, we explore the startup phase. During this exciting part of the project, it’s critical to work with a strategic plan. Below we share a phased format with specific steps to get you from virtual commissioning to the site acceptance test to product qualification.
Starting up your greenfield factory
Developing a greenfield site and bringing it online can take three to five years, so we’ve broken down the journey into four phases and 12 steps. When you arrive at the startup phase after so much work to get there, it’s a huge milestone. But now more than ever, this phase requires good planning and thorough execution. Each step of the way, from virtual commissioning to product qualification, must follow a strategic plan to start up with success.
Step 7: Commissioning
Commissioning is the process of ensuring that all equipment, systems, and components of a factory are installed, operational, and tested according to the design and requirements. If the testing and debugging of complex manufacturing control systems is time-consuming, a ‘virtual’ commissioning strategy using a digital twin can be developed to reduce startup risk and timeline.
Planning
As with many other aspects of the greenfield factory journey, successful virtual commissioning requires good planning, done well in advance of the commissioning activities. Define and prepare documentation early in the process, including test plans and test procedures to be executed during commissioning, required checklists, and drawings. Obtain an accurate set of “as-built” drawings to reflect the actual location, hookup, and configuration of equipment in the field.
Involve operations team
It is also important for factory startups to involve the team that will own and operate the factory equipment in the virtual commissioning process. It’s a great opportunity to train operations on the systems and become familiar with the operational complexities before taking over the systems, ultimately enabling a more seamless transition to factory startup.
Acceptance testing
As production systems are brought online, it is critical to properly test their function and operation to ensure they are running and performing as designed. Now’s the time to find out if something is not working correctly, responding properly, or failing over as planned when there is an abnormal event. Discovering a problem after the factory has started up will reduce productivity, momentum, and credibility. But successful site acceptance testing starts well before systems are hooked up and installed. It starts during the procurement process where acceptance test plans and criteria are agreed upon between the owner and original equipment manufacturer (OEM), in advance of signing contracts or placing purchase orders (POs).
- Factory acceptance testing (FAT)
In some cases, it is wise to perform factory acceptance testing (FAT) at the OEM’s factory prior to shipment of the systems/equipment, especially for complex systems where issues are much easier and cheaper to fix before they leave the factory. - Site acceptance testing (SAT)
When the equipment is ready to start up, it may be necessary to clean and flush pipes, pressure test systems, and perform leak testing. Perform a run-in period for motors and pumps to verify vibration and heating/cooling. For electrical systems, commissioning activities consist of panel energization, communication checks, loop checks (internal and external), and wiring verification. Mechanical commissioning confirms the proper function of mechanical systems first without process fluids, then with process fluids and chemicals to confirm the proper operation. - Integration testing
Integration testing may be necessary to verify and confirm operation of the equipment within the larger set of control and monitoring systems. Check field devices to see that they are correctly reflected on dashboards and can be controlled from the central control location. This enables all equipment to be tested together as a system for the first time, from automation to fault scenarios to end-to-end communications.
Documentation and data handover
As the in-service date nears, owners typically receive all operations manuals, configuration information, diagrams, etc. for the equipment and systems, as well as information on each asset, the hierarchy of installation, nameplate data, software licenses, preventive maintenance requirements, and warranty information.
This engineering data is critically important to a successful factory startup, providing significant value for an accelerated startup and long-term operational efficiency. From understanding load capacities to effectively monitoring and predicting equipment maintenance needs, the engineering data provided by OEMs and system integrators helps minimize surprises and optimize the production process.
Step 8: Startup
Starting up a new factory is very exciting. It’s a huge milestone and reason for celebration. But unless the startup is well-planned, you can quickly run into challenges. Focus on these key areas to drive startup success.
People
When starting up a factory in a new location, you need a team of employees who are trained and ready to operate equipment, run production, and monitor operations. Building that team may seem daunting, particularly when starting from scratch with the local workforce. But the right strategies can help accelerate hiring, training, and preparation for the core team to start up the factory.
- Hire key positions early
Hire key positions early in the greenfield factory journey. Getting them in the door during the initial stages of the process and letting them come along for the ride through the equipment installation and commissioning phases goes a long way in building their knowledge, getting them trained, and instilling a sense of ownership. - Leverage existing factories for training
Hire key employees early and train them at a similar factory. Embedding them in existing operations to shadow people with a similar job role is a great way to train new hires quickly and bring them up to speed. They will learn details about mature processes and develop relationships that can be leveraged to establish best practices across the factory network. If a digital twin of the asset exists, training can even begin in a virtual environment.
- Relocate trained talent
You can also de-risk startup plans by relocating key experienced employees to help run the new factory for an extended period, such as one to two years. - Partner with local colleges
Establish relationships early with local colleges to build support, tailor curriculum to specific needs, and develop a pipeline of skilled workers.
Manufacturing applications
While planning and building the factory, focus on helping ensure all systems are ready for operations to start up. If you start fresh with new, modern manufacturing systems, plan carefully to define requirements, select the right systems, and understand what it will take to get them installed, integrated, and tested. This can include the design of OT and IT infrastructure required to support the manufacturing systems, as well as what is needed for integration with enterprise systems. In today’s dynamic business environment, it is important to design for technical agility to enable business agility. Consider cybersecurity, scalability, connectivity, and user experience when designing your modern solution architecture. Designing and deploying manufacturing applications in the context of your workforce, processes, and desired manufacturing outcomes can lead to optimized human:machine interactions and more seamlessly orchestrated workflows.
You could also build a staging environment to give teams the opportunity to set up, pilot, and qualify the systems and equipment and test their functionality and integration before running them in the new factory. This lab environment can also serve as a training facility for operations and engineering personnel.
Startup strategy
When the first product is ready to be moved into production, it may be advantageous to start a “pipe cleaner” production order to exercise the production systems in tandem to uncover hiccups and gaps. Exposing these issues early means they can be addressed sooner.
The initial output of the new factory will likely be low quality and yield until enough volume is produced and adjustments can be made, so this should be incorporated into the plan for production tests.
For longer production processes, manufacture material up to a certain point at an existing factory, then transfer the material to continue at the new factory. This approach allows earlier learning and tuning of processes that come much later in the overall manufacturing cycle.
Step 9: Product qualification
Product qualification and/or process certification is sometimes required in sensitive industries and marketplace areas where a product failure could have serious consequences. When a formal product qualification is not a specific requirement, this process is often overlooked and undervalued, even though it is a great vehicle to quickly establish confidence and credibility in the new revenue stream.
Aligning the organization
A good product qualification plan will help ensure stakeholders are aligned. Otherwise, engineers who perform product qualification often don’t understand requirements, test standards, or methodology. This may be due to a lack of specified requirements, misunderstanding regulatory requirements, underestimating the effort after release to production, trying to go too fast, or trying to do too much with too few qualification lots. If you fail a product qualification test, you must start over again, wasting valuable time and delaying the factory’s ability to produce and ship revenue.
Establishing a product qualification plan
A good product qualification plan creates a line of sight from starting the qualification lot to beginning commercial production. The process includes identifying potential failure modes and mechanisms of the new processes/equipment. Next, the qualification lots or samples are subject to the appropriate reliability stresses to accelerate potential failure mechanisms. This may be done in-house or contracted to a third-party lab or certification body. Lastly, the qualification lots or samples are tested to determine if they are still acceptable after completing the reliability stresses.
How Deloitte can help the greenfield factory journey
With deep expertise across industries, Deloitte has helped many leading global companies develop a greenfield site. No matter where you are in the journey, we can help you get back on track and realize your ultimate greenfield goals, using new methodologies that reduce risk, improve performance, and save time and money.
As a strategic partner, our smart manufacturing team can also fill knowledge gaps across tax strategy, consulting, financial advisory, risk advisory, and business process transformation. Contact us today to learn how we can work together to bring your greenfield vision to life.
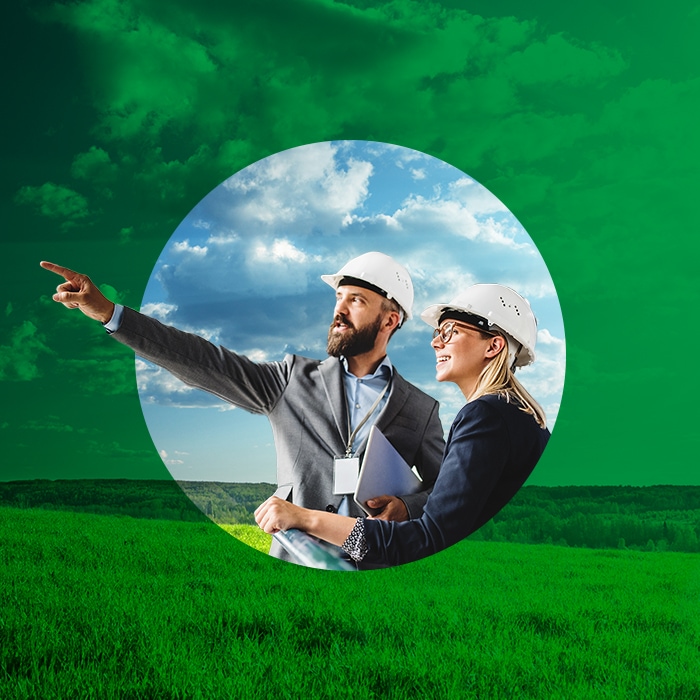
Optimize your Greenfield smart factory with Deloitte
Interested in learning more? Complete the form below and we’ll get in touch.
Get in touch

Principal, Deloitte Consulting LLP
Smart Manufacturing Senior Commercial Advisor
${fourth-leader-name}
${fourth-leader-title}
${fourth-leader-additional-info}
Recommendations
Predictive maintenance and the smart factory
Connecting machines to reliability professionals
How to secure OT and IT in cybersecurity manufacturing
Six cybersecurity challenges for manufacturers and how to address them.