The greenfield factory journey: Phase 4 has been saved
Perspectives
The greenfield factory journey: Phase 4
Ramp: Optimization with lean manufacturing
In the final installment of our four-part article series detailing Deloitte’s greenfield factory journey, we explore the ramp phase—when you start seeing the fruits of your labor. From optimization to lessons learned, this stage focuses on lean manufacturing and continuous improvement methods such as Six Sigma, Kaizen, and the Theory of Constraints.
Ramping your greenfield factory
Developing a greenfield site and bringing it online can take three to five years, so we’ve broken down the journey into four phases and 12 steps. This final phase, ramp, is filled with excitement to see months and years of hard work come to life. Now firmly in the “program oversight” portion of the project, ramping up a factory may feel like the end of a long journey, but it’s just the beginning of what’s next for your organization.
Step 10: Ramp
There’s something special about being part of a startup team ready to ramp up a factory. Everyone is eager to see the factory succeed and willing to put in extra effort to make it happen. But ramping up a factory is not without its challenges. There’s a lot of work and planning required to reduce the number of unexpected problems that may arise.

If needed to produce a high volume quickly to hit a tight product launch window, installing and validating the second-of-a-kind equipment and fixtures will be critical. One of the most likely ramp killers is when only one tool can perform a critical process step and that tool is down. Having a second run path for production to continue will help keep work moving through the factory.

Technicians usually spend a lot of time making the first line work, deprioritizing additional lines. New lines can introduce new problems, so qualifying them should be done systematically to reduce variables. When bringing up a new line and equipment, use the same processes, components, and parts as the original. Assign the same engineers, technicians, and operators to subsequent lines to use their learnings and enable them to replicate the performance of previously qualified lines.

As production is scaled to meet the launch schedule, keep an eye on incoming parts and materials supply. Many vendors will fail to deliver the volume and quality when it’s needed most. It’s important to hold vendors accountable by making sure they have a plan to ramp their production. Have them build agility into their schedule to accommodate adjustments to mitigate risk. Vendors should be able to prove they can scale their own production capacity and delivery while maintaining quality control.

Ramping up large, complex factories is more effective when broken up in waves or batches. It enables integrated planning, coordination, and smoother execution of all the required equipment, production lines, raw materials, consumables, and staff to be grouped into individual batches. This phased approach is more manageable, enables acceleration of the ramp timeline, and leads to a more optimized operation at full capacity.

As the volume of work-in-process (WIP) increases, dashboards and reporting become more important. WIP status, equipment performance, production volume, line yield, and other metrics and key performance indicators (KPIs) enable operators, engineers, and managers to quickly assess the health of operations and respond quickly to issues. Ensuring that you have good systems that capture data and dashboards that report in the right way will make the difference between a successful ramp and missing critical ramp targets.
Step 11: Manufacturing optimization and the smart factory journey
As the factory ramps and production volume targets are achieved, efforts begin to shift toward optimization. Areas of focus often include decreasing overall factory throughput time, reducing costs, and improving yield and quality.
While some key considerations are outlined in this step of the greenfield factory journey, manufacturing optimization is never complete. There are many ways to enhance, develop, increase, progress, and upgrade manufacturing performance. The opportunities are seemingly endless—and thus the adventure of continuous improvement begins.
Continuous improvement
The continuous improvement process is simple, but few companies do it well due to not establishing the discipline to operationalize the continuous improvement process and make it a formal part of their culture. The following are various methods that can be used to formalize continued improvement.
- Plan-Do-Check-Act (PDCA)
PDCA is a four-step methodology used to identify, test, and implement changes to improve a manufacturing process. It focuses on measuring and analyzing results to identify the actions needed for improvement efforts. - Kaizen lean manufacturing
Japanese for “improvement,” the terms “kaizen” and “continuous improvement” are often used interchangeably. The Kaizen manufacturing method focuses on making incremental changes in the factory that are often easy to implement and track. - Six Sigma manufacturing
Six Sigma is a manufacturing method designed to improve the quality of processes by removing defects and minimizing process variability, using data and statistics to analyze processes, and identifying areas for improvement. - Lean manufacturing
This approach is used to optimize production processes by eliminating waste and focusing on creating value for the customer. It is based on two core principles: continuous improvement and respect for people. - Theory of Constraints (TOC)
The Theory of Constraints concept focuses on identifying the biggest bottleneck in the factory to improve it. This concept hinges on the idea that identifying and addressing the biggest system constraint is the fastest path to improvement and continuous growth.
Implementing and formalizing the continuous improvement process takes commitment, ongoing effort, and continued practice to make a real difference. With the right strategy, tools, and leadership, efforts to optimize the factory will pay big dividends.
The smart factory journey
While planning and building a new greenfield factory, you can embark on a parallel trek—the smart factory journey. The specific elements of a digital thread within manufacturing will be different for each organization, but there are key characteristics that are common. A review of key characteristics affords manufacturers a chance to imagine the possibilities, ultimately leading to improved productivity and greater competitive advantage.
- Connected
Smart factories require the underlying equipment, processes, and materials to be connected to generate data regarding current conditions and real-time status. This data then becomes the foundation for all other smart factory characteristics. - Transparent
Real-time alerts, notifications, tracking, and performance monitoring open the window of understanding into what is really happening, thereby enabling new, significant insights and opportunities for improvement. - Proactive
In a factory with proactive systems and processes, employees and systems can anticipate and act before issues or challenges arise or become significant, rather than simply reacting to them after they occur. - Optimized
An optimized smart factory has matured key capabilities such as improved tracking, dynamic scheduling, increased uptime, and improved quality, as well as minimized waste. - Agile
A flexible, agile factory allows for easy and rapid adaptation to schedule and product changes with minimal intervention.
Far from being an “end state,” the smart factory is an evolving solution as the industry forges ahead to integrate Industry 4.0 together with a software-defined future. It is an unending call for creative thinking and imagining the possibilities. Investing in smart factory capabilities and applying principles of software-defined manufacturing can enable manufacturers to develop a competitive advantage in an ever-more complex and rapidly shifting ecosystem.
Step 12: Lessons learned and what’s next
Manufacturing leaders may be tempted to sit back and celebrate their success after completing the ramp and optimization of the factory. While it’s important to mark the success of these milestones, take advantage of the collective knowledge the core team developed during the journey.
${header-title}
${column1-large-text}
Capture lessons learned
Good leaders will capture best practices, standards, and lessons learned about the greenfield factory journey, particularly if the journey may be repeated in the coming years. To facilitate a future project, add information to an updated playbook to educate new teams and facilitate communication.
${column2-large-text}
Share the knowledge
Learning occurs on every project, and the greenfield factory journey is no different. Share knowledge through stand-up meetings, after-action reviews, “lunch & learns,” and more to prevent repeating the same mistakes. Implement best practices to improve current and future projects.
${column3-large-text}
${column3-title}
${column4-large-text}
${column4-title}
Explore case studies

Client Background
A startup business needed to design and build their first manufacturing plant but had limited experience with manufacturing. The client sought help to design their production operations leading to full commercialization and templatization of the factory design to scale globally as their business grows.
Summary
Deloitte partnered with the client to develop a multi-year greenfield smart factory conceptual design, operating model, and foundational technology landscape including key vendors and solutions that could achieve the company’s short- and long-term growth goals.
- Simulated and iterated factory designs using dynamic assumptions and various product mix/scale scenarios, with models of key production metrics:
- Asset performance to identify most suitable production technologies
- Downtimes to model constraints, while minimizing assets and costs
- Workforce needed to operate and maintain assets, and move material
- Researched physical and digital technology vendors and products to optimize operational efficiency while reducing total costs
- Cored vendors on functional fits, strategic fits, scalability and costs
Impact
- Designed manufacturing capacity ramp plan to accommodate significant capacity increases over time
- Sequenced assets and IT systems optimally for maximizing ROI
- Built leadership confidence in executable vision
- Designed quality controls for efficient production
- Built strong foundation for product technology platforms to define manufacturing operating system via core technology recommendations and template development

Client Background
An advanced manufacturer needed construction program advisory services to conduct site selection analysis and incentives negotiations for building a new US plant to expand the client’s network of global manufacturing facilities.
Solution
Deloitte partnered with the client’s global and US project leadership teams on business case development, financial modeling, incentives negotiations, and architecture, engineering, and construction selection. The teams began with 100 locations and used a multi-phase, down-select approach to determine the most suitable site for the new US plant.
- Assessed business case and project needs to extract key assumptions, plan the project calendar, and gather critical location specifications such as labor quality and availability, real estate and utility infrastructure, and business, operating, and regulatory environments; resulted in 35 suitable sites.
- Conducted location analysis with field investigations of the 35 sites to assess technical suitability, including topography, layout, utility infrastructure, community support, labor force and regulations, air permitting regulations, natural disaster risk, and port, highway, and airport access; retained nine locations for negotiations.
- Performed field site due diligence of the nine remaining locations to locate potential flaws by inspecting soil conditions and site access, reviewing utility provisions and proposals for capacity expansion, and analyzing local transportation infrastructure and training and recruitment capabilities; requested three communities to submit proposals for consideration.
- Supported negotiations with a structured approach that entailed multiple rounds of talks with key state, county, city, utility, and railroad officials, foreign plant tours and meetings with client executives, and development of the project Memorandum of Understanding and supporting documents.
- Created unmatched incentive package working in tandem with the state and local community, including utility, rail, training, and transportation grants and funding and elimination of corporate income taxes, and developed a program incentives playbook outlining administrative steps to realize incentives value; selected final location for the new US plant.
Impact
- Executed successful site selection for US expansion
- Decreased risk and optimized long-term cost profile
- Negotiated one of the highest-value state and community incentive packages
- Reduced one-time costs to drive more funds into onsite improvements
- Established scalable site and workforce development at no cost to accommodate growth
How Deloitte can help the greenfield factory journey
With deep expertise across industries, Deloitte has helped many leading global companies develop a greenfield site. No matter where you are in the journey, we can help you get back on track and realize your ultimate greenfield goals, using new methodologies that reduce risk, improve performance, and save time and money.
As a strategic partner, our smart manufacturing team can also fill knowledge gaps across tax strategy, consulting, financial advisory, risk advisory, and business process transformation. Contact us today to learn how we can work together to bring your greenfield vision to life.
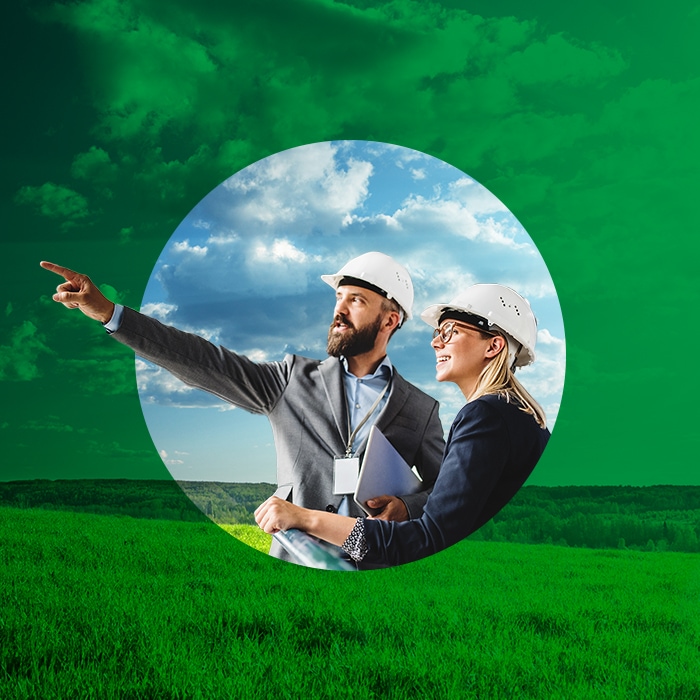
Explore the full greenfield factory journey
Thank you for joining us on the greenfield factory journey! If you missed previous articles on planning, executing, and startup—or want to read them again—visit our homepage.
Optimize your Greenfield smart factory with Deloitte
Interested in learning more? Complete the form below and we’ll get in touch.
Get in touch

Principal, Deloitte Consulting LLP
Smart Manufacturing Senior Commercial Advisor
${fourth-leader-name}
${fourth-leader-title}
${fourth-leader-additional-info}