The greenfield factory journey has been saved
Perspectives
The greenfield factory journey
12 steps to building a successful greenfield site
As reshoring gains traction amid worldwide disruption, greenfield manufacturing sites are popping up left and right. What strategic considerations should guide the process? This four-part article series details Deloitte’s greenfield factory journey and the steps organizations should take to successfully realize the vision for a new plant.
A rise in reshoring calls for greenfield manufacturing sites
Seismic shifts in the geopolitical and macroeconomic landscape in recent years have forced manufacturers to rethink their approach to fulfilling demand. While global factory networks were commonplace during the last few decades, recent events such as COVID-19, supply chain disruptions, shortage of skilled labor, and inflation have created unprecedented challenges.
To address these challenges, manufacturers are increasingly considering reshoring and building new factories in the United States. Building a greenfield factory can increase overall manufacturing capacity, create redundant supply, reduce unit costs through increased automation, improve quality, and potentially reduce time to market for new products.
A well-developed strategy for a greenfield factory can ensure a digital thread foundation is built in from the start. Advanced digital technologies such as sensors, wearables, and robotics can unlock additional value from the new factory investment. And incorporating exponential technologies like Internet of Things (IoT), cloud, machine learning, and artificial intelligence can turn advanced data into actionable insights.
Building a new factory may be an obvious investment choice, but where to start? In this article series, we dive into each critical phase of the greenfield factory journey, outlining how Deloitte can help develop the right strategy and provide oversight while building a new plant.
Explore each phase of the greenfield factory journey
Bringing a greenfield site online can take three to five years, so we’ve broken down the journey into four phases and 12 steps. Explore each article to better understand the process and how Deloitte can strategically help guide the creation of your greenfield plant.

Arguably the most important phase of the process, planning is where an organization defines its objectives and strategy, selects the location of the greenfield plant, and begins a detailed design of the factory. This phase takes approximately six to 24 months.
Read more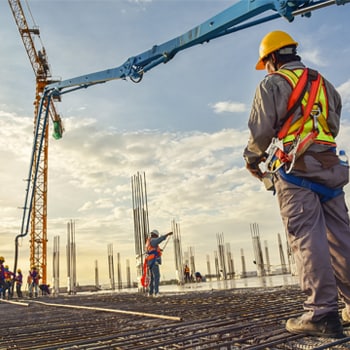
Execution of your greenfield vision starts with sourcing and procurement. From there, construction begins, with heavy oversight and project management throughout. Once the greenfield site is built, equipment installation and design begin. This phase takes approximately 12 to 36 months.
Read more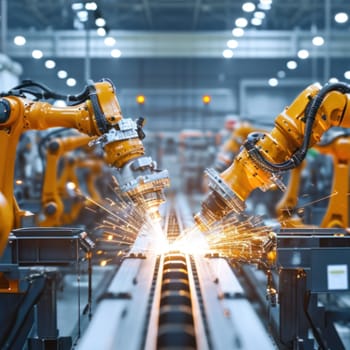
Startup is where you can really see the pieces come together, beginning with commissioning. Once the systems and equipment are tested, it’s time to start up your new factory! If necessary, product qualification also takes place in this phase, which takes approximately six to 12 months.
Read more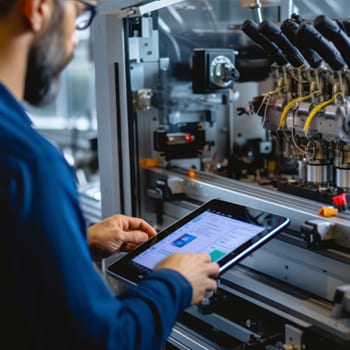
The final phase of the process is ramping up your greenfield factory. Once scaled and launched, the focus shifts to optimization—a part of your journey that is never complete. Finally, it’s time to reflect on lessons learned and prepare for what’s next. This phase takes approximately six to 24 months.
Read moreHow Deloitte can help the greenfield factory journey
With deep expertise across industries, Deloitte has helped many leading global companies build a greenfield site. No matter where you are in the journey, we can help you get back on track and realize your ultimate greenfield goals, using new methodologies that reduce risk, improve performance, and save time and money.
As a strategic partner, our Smart Manufacturing team can also fill knowledge gaps across tax strategy, consulting, financial advisory, risk advisory, and business process transformation. Contact us today to learn how we can work together to bring your greenfield vision to life.
Explore case studies

Client Background
A semiconductor company, historically focused on maximizing the amount of equipment in its factory, was seeking new ways to expand its manufacturing facilities, building them for agility over output. Each piece of equipment required a custom design package for tool hookup, a lengthy and costly process. To accelerate installation and the start of operations, the manufacturer needed new automated optimization methods that would balance equipment density needs with standardized tool hookup packages.
Solution
The manufacturer needed to construct a greenfield fabrication plant quickly, while designing the factory layout to improve quality process and space utilization. Deloitte created a working solution capable of inputting factory layout requirements into an automated platform to simulate layout scenarios and identify the optimal baseline layout of a fabrication plant. The solution provides better visibility of the new floor parameters, creating a clear understanding of the scope and impact of demand changes and how to meet operational needs. Deloitte partnered with the company to:
- Collect key layout requirements: Gathered details, such as tool types, factory size, and design constraints, and fed them into the solution to create a baseline, spatial digital twin model of the fabrication plant, sub-fabrication area, and support structures.
- Automate the model: Produced possible iterations of the plant layout, including tool density details, possible tools per square feet, and cost summaries; facilitated high-speed simulation of thousands of potential layouts and ability to view pros and cons of each option.
- Allow for new potential layouts: Created the possibility to input design iterations into an AI-driven optimizer that can prioritize layouts based on changing inputs and optimization of criteria, providing the ability to standardize construction of a greenfield fabrication layout, allow for more tools and better tool orientation, and simplify complexity with less customized hookup packages.
- Manage stakeholders: Aligned construction and tool installation teams with the contractors required for execution.
Impact
- Produces a fully functional 3D digital twin model of fabrication and sub-fabrication areas
- Accelerates time to develop an optimized fabrication design from months to days
- Increases standardization in fabrication layout for more cost-effective construction for base build and tool installation

Client Background
A startup business needed to design and build their first manufacturing plant but had limited experience with manufacturing. The client sought help to design their production operations leading to full commercialization and templatization of the factory design to scale globally as their business grows.
Summary
Deloitte partnered with the client to develop a multi-year greenfield smart factory conceptual design, operating model, and foundational technology landscape including key vendors and solutions that could achieve the company’s short- and long-term growth goals.
- Simulated and iterated factory designs using dynamic assumptions and various product mix/scale scenarios, with models of key production metrics:
- Asset performance to identify most suitable production technologies
- Downtimes to model constraints, while minimizing assets and costs
- Workforce needed to operate and maintain assets, and move material
- Researched physical and digital technology vendors and products to optimize operational efficiency while reducing total costs
- Cored vendors on functional fits, strategic fits, scalability and costs
Impact
- Designed manufacturing capacity ramp plan to accommodate significant capacity increases over time
- Sequenced assets and IT systems optimally for maximizing ROI
- Built leadership confidence in executable vision
- Designed quality controls for efficient production
- Built strong foundation for product technology platforms to define manufacturing operating system via core technology recommendations and template development

Client Background
An advanced manufacturer needed construction program advisory services to conduct site selection analysis and incentives negotiations for building a new US plant to expand the client’s network of global manufacturing facilities.
Solution
Deloitte partnered with the client’s global and US project leadership teams on business case development, financial modeling, incentives negotiations, and architecture, engineering, and construction selection. The teams began with 100 locations and used a multi-phase, down-select approach to determine the most suitable site for the new US plant.
- Assessed business case and project needs to extract key assumptions, plan the project calendar, and gather critical location specifications such as labor quality and availability, real estate and utility infrastructure, and business, operating, and regulatory environments; resulted in 35 suitable sites.
- Conducted location analysis with field investigations of the 35 sites to assess technical suitability, including topography, layout, utility infrastructure, community support, labor force and regulations, air permitting regulations, natural disaster risk, and port, highway, and airport access; retained nine locations for negotiations.
- Performed field site due diligence of the nine remaining locations to locate potential flaws by inspecting soil conditions and site access, reviewing utility provisions and proposals for capacity expansion, and analyzing local transportation infrastructure and training and recruitment capabilities; requested three communities to submit proposals for consideration.
- Supported negotiations with a structured approach that entailed multiple rounds of talks with key state, county, city, utility, and railroad officials, foreign plant tours and meetings with client executives, and development of the project Memorandum of Understanding and supporting documents.
- Created unmatched incentive package working in tandem with the state and local community, including utility, rail, training, and transportation grants and funding and elimination of corporate income taxes, and developed a program incentives playbook outlining administrative steps to realize incentives value; selected final location for the new US plant.
Impact
- Executed successful site selection for US expansion
- Decreased risk and optimized long-term cost profile
- Negotiated one of the highest-value state and community incentive packages
- Reduced one-time costs to drive more funds into onsite improvements
- Established scalable site and workforce development at no cost to accommodate growth
Optimize your Greenfield smart factory with Deloitte
Interested in learning more? Complete the form below and we’ll get in touch.
Get in touch

Principal, Deloitte Consulting LLP
Smart Manufacturing Senior Commercial Advisor
${fourth-leader-name}
${fourth-leader-title}
${fourth-leader-additional-info}
Recommendations
Manufacturers prioritize targeted investments in their digital and data foundation to boost innovation and tackle ongoing skills gap and supply chain challenges
Reshoring or localization on your mind?
Manufactures can upgrade to smart factory facilities when reshoring. This means making critical decisions about facility investments, strategy, technology, and people.