The greenfield factory journey: Phase 2 has been saved
Perspectives
The greenfield factory journey: Phase 2
Managing and executing a greenfield manufacturing project
In part 2 of our four-part article series detailing Deloitte’s greenfield factory journey, we explore the execution phase, from industrial procurement to construction to equipment install. During this phase, it’s crucial to manage the project closely to ensure your factory is completed on time.
Executing your greenfield factory
Developing a greenfield site and bringing it online can take three to five years, so we’ve broken down the journey into four phases and 12 steps. When managing a large-scale manufacturing project, this second phase—executing—is key to keeping the overall greenfield factory project on time and on budget. Execution starts with sourcing and industrial procurement, as this enables all tangible activities through construction and commissioning. This second phase takes an average of 12 to 36 months to complete.
Step 4: Industrial procurement
Manufacturing organizations embarking on a greenfield factory journey may not appreciate the magnitude of the effort required to effectively execute and manage a large-scale project. Consider tapping into additional resources in these following areas.
Sourcing
To establish the new manufacturing capacity, a broad range of materials and supplies must be procured, from construction materials to industrial equipment to new consumables. A sourcing strategy can help address concerns, such as procuring long lead-time materials early, pursuing multiple sources to de-risk the supply and delivery of critical items, and using suppliers who are nearby, which may reduce costs and create goodwill with the local area.
Tapping into local service vendors is time-consuming and may require in-person meetings and field visits. If organizations want to onboard a new supplier, they must gather pertinent information and submit it for internal approval and system setup. Depending on the size of the greenfield project, its success may depend on supplementing the current workforce with additional resources who can handle multiple supplier onboardings.
Contracts
If an architect and/or a general contractor has been identified to build the factory, there is a significant effort required to negotiate a contract and perform a legal review to protect the company. When other new suppliers are identified to provide goods and services, a Master Services Agreement is usually written up. The process of writing these agreements and getting stakeholder approval can take a significant amount time, and organizations should supplement internal staff with contractors who can develop, review, and approve contracts quickly.
Funding
When building a greenfield factory, a high-level budget is usually locked in. However, every project and sub-project supporting the factory typically needs review and final approval. Depending on the processes for securing and approving capital expenditures (CapEx), there may be a significant amount of work required to build and approve requests. Bringing in outside help to facilitate this mountain of work may be necessary. It may also help to have an outside perspective to identify opportunities to streamline the CapEx approval processes so it doesn’t become a bottleneck to executing work. There may also be opportunities to leverage alternate financing options, such as federal grant funding.
Step 5: Construction
There are many things that can go wrong in the construction phase, from unrealistic expectations to long lead times for materials and equipment, to lack of skilled labor and availability of specialized equipment. Developing the right strategy will help mitigate risks and improve the project performance.
Design and build
An integrated design and build approach offers numerous advantages over a traditional waterfall or sequential method in which design is done first, then construction follows. Using the same firm for both design and build means you get the expertise, commitment, and availability of resources for construction, along with the skill sets of an architect and engineer for design. Benefits of streamlining this process include simplifying designing, planning, and building processes through a single point of contact; fewer disputes, interruptions, and delays, making it easier to stay on schedule; and lower overall costs.
Prefabrication and offsite construction
Another great time and cost savings approach is to identify opportunities up front where fabrication of subassemblies, sections, modules, etc. can be done offsite, then brought onsite for final installation.
One of the biggest advantages of prefabrication and offsite construction is the ability to reduce project timelines. Traditional construction methods often involve sequential tasks or processes that can lead to delays caused by logistics, weather, and many other factors. Reducing the labor onsite can drive significant savings, as this type of work can be done in a controlled environment where there are accommodations for workers and weather conditions have minimal impact.
Plus, the assembly process on the construction site is more efficient, as the prefabricated components are designed to fit together seamlessly with quicker install. This expedites the overall construction process, enabling projects to be completed in a fraction of the time it would take using conventional methods.
Project management
Another key to a successful construction phase is to have good factory project management and strong project governance. Successful project management is built on the fundamentals of planning and communicating.
A detailed project plan is important, but it is only as good as the data and assumptions used to build it. Building a successful project plan requires not only a solid understanding of the tasks, dependencies, and resources required, but also excellent communication and collaboration with subcontractors, trades, and procurement professionals to make sure each task is understood and grounded in lead times and required versus available resources.
This entails daily, hands-on interaction on the construction site. Project managers who work remotely or spend most of their time away from the manufacturing site will be too disconnected from the challenges and realities in the field. At a minimum, daily walkthroughs must be conducted to understand issues firsthand and drive accountability. Failure to effectively plan is mostly due to the lack of engagement with teams in the trenches.
Step 6: Manufacturing equipment install
The final step of the execution phase is equipment install. This is where the factory really starts to come to life, and a detailed plan is crucial for managing the project from design to staging to final move-in.

Depending on the complexity of the manufacturing equipment that needs to be installed, it may be necessary to create a detailed “design package” for each piece of equipment, covering everything from custom pedestals to electrical hookups to drains and waste systems. In some cases, manufacturing equipment may also need to be interfaced with other support equipment or automation systems.

The best practice in tool hookup methodology is to design standard equipment installation modules that are prebuilt or manufactured offsite. This approach enables significant schedule acceleration and requires less onsite labor. It also enables greater design flexibility in making equipment layout changes in the future. Consistent layouts for valves, gases, gauges, meters, filters, and sensors make long-term maintenance easier while taking the guesswork out of safety shutdown procedures.

A successful strategy for large manufacturing projects is to use local warehousing space as a buffer for equipment that will be installed in the factory. Often original equipment comes from overseas on ocean cargo ships that must pass through customs and be inspected before arrival at the site. Planning to stage this equipment in a warehouse in the local area allows for detailed scheduling and just-in-time arrival at the factory dock once the factory reaches the “ready for equipment” milestone.

To further accelerate the installation timeline, a section of the new factory (or an offsite location) could be set up to preassemble equipment, begin integration testing, and start the qualification process. It may also be helpful to use this approach for hands-on training of key personnel in advance of hookup, and to set up in the final factory location, accelerating the overall time to ramp and production.

It is crucial to have a well-planned equipment installation. There are significant dependencies on “base build” or supply systems (mechanical, electrical, HVAC) and readiness of process lateral systems (water, drain, chemicals) that need to be mapped out. To avoid a bottleneck at the dock, a detailed plan around dock time may be necessary. Some equipment may also be extremely heavy or expensive, so the move-in path may need to be well orchestrated or involve professional rigging companies.
Explore case studies

Client Background
A startup business needed to design and build their first manufacturing plant but had limited experience with manufacturing. The client sought help to design their production operations leading to full commercialization and templatization of the factory design to scale globally as their business grows.
Summary
Deloitte partnered with the client to develop a multi-year greenfield smart factory conceptual design, operating model, and foundational technology landscape including key vendors and solutions that could achieve the company’s short- and long-term growth goals.
- Simulated and iterated factory designs using dynamic assumptions and various product mix/scale scenarios, with models of key production metrics:
- Asset performance to identify most suitable production technologies
- Downtimes to model constraints, while minimizing assets and costs
- Workforce needed to operate and maintain assets, and move material
- Researched physical and digital technology vendors and products to optimize operational efficiency while reducing total costs
- Cored vendors on functional fits, strategic fits, scalability and costs
Impact
- Designed manufacturing capacity ramp plan to accommodate significant capacity increases over time
- Sequenced assets and IT systems optimally for maximizing ROI
- Built leadership confidence in executable vision
- Designed quality controls for efficient production
- Built strong foundation for product technology platforms to define manufacturing operating system via core technology recommendations and template development

Client Background
An advanced manufacturer needed construction program advisory services to conduct site selection analysis and incentives negotiations for building a new US plant to expand the client’s network of global manufacturing facilities.
Solution
Deloitte partnered with the client’s global and US project leadership teams on business case development, financial modeling, incentives negotiations, and architecture, engineering, and construction selection. The teams began with 100 locations and used a multi-phase, down-select approach to determine the most suitable site for the new US plant.
- Assessed business case and project needs to extract key assumptions, plan the project calendar, and gather critical location specifications such as labor quality and availability, real estate and utility infrastructure, and business, operating, and regulatory environments; resulted in 35 suitable sites.
- Conducted location analysis with field investigations of the 35 sites to assess technical suitability, including topography, layout, utility infrastructure, community support, labor force and regulations, air permitting regulations, natural disaster risk, and port, highway, and airport access; retained nine locations for negotiations.
- Performed field site due diligence of the nine remaining locations to locate potential flaws by inspecting soil conditions and site access, reviewing utility provisions and proposals for capacity expansion, and analyzing local transportation infrastructure and training and recruitment capabilities; requested three communities to submit proposals for consideration.
- Supported negotiations with a structured approach that entailed multiple rounds of talks with key state, county, city, utility, and railroad officials, foreign plant tours and meetings with client executives, and development of the project Memorandum of Understanding and supporting documents.
- Created unmatched incentive package working in tandem with the state and local community, including utility, rail, training, and transportation grants and funding and elimination of corporate income taxes, and developed a program incentives playbook outlining administrative steps to realize incentives value; selected final location for the new US plant.
Impact
- Executed successful site selection for US expansion
- Decreased risk and optimized long-term cost profile
- Negotiated one of the highest-value state and community incentive packages
- Reduced one-time costs to drive more funds into onsite improvements
- Established scalable site and workforce development at no cost to accommodate growth
How Deloitte can help the greenfield factory journey
With deep expertise across industries, Deloitte has helped many leading global companies develop a greenfield site. No matter where you are in the journey, we can help you get back on track and realize your ultimate greenfield goals, using new methodologies that reduce risk, improve performance, and save time and money.
As a strategic partner, our smart manufacturing team can also fill knowledge gaps across tax strategy, consulting, financial advisory, risk advisory, and business process transformation. Contact us today to learn how we can work together to bring your greenfield vision to life.
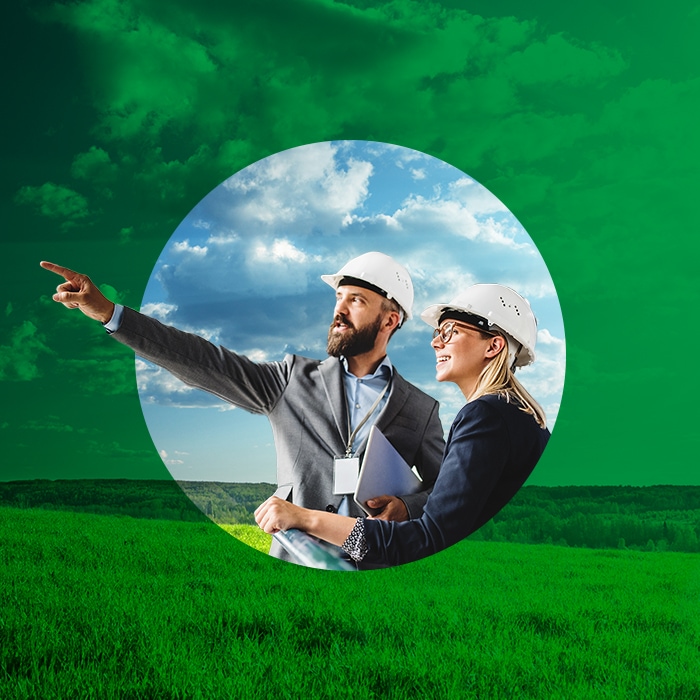
Explore phase 3 of the greenfield factory journey
Our next article dives into phase 3 of the greenfield factory journey: startup. Now that your factory is built and your equipment is in place, it’s time to bring it to life, from commissioning to startup to product qualification.
Optimize your Greenfield smart factory with Deloitte
Interested in learning more? Complete the form below and we’ll get in touch.
Get in touch

Principal, Deloitte Consulting LLP
Smart Manufacturing Senior Commercial Advisor
${fourth-leader-name}
${fourth-leader-title}
${fourth-leader-additional-info}
Recommendations
Manufacturers are optimistic about the industrial metaverse and are exploring ways it can create value in their talent, supply chain, customer, and production ecosystems, reveals the 2023 Deloitte and Manufacturing Leadership Council (MLC) Industrial Metaverse Study.
Optimize operating models with smart manufacturing
Smart Factory applications are transforming the future of factories. See how smart manufacturing can help accelerate organizations to a smarter operating model.