Making the case for inventory optimization has been saved
Perspectives
Making the case for inventory optimization
How to use inventory analytics to your advantage
The days of inventory being considered an asset with expected rate recovery are long gone. Inventory investment is increasingly under scrutiny by both management and the utility commissions—meaning that inventory optimization needs to be effectively managed and budgeted.
The cost of carrying inventory
Inventory isn’t free. Chances are, you’re holding more inventory than is in your rate base, possibly diminishing your earnings potential through regulatory lag and O&M carrying cost expense.
Chief among the cost of inventory is its ongoing carrying costs—including warehouse facility costs, labor costs associated with managing inventory, and recurring costs related to taxes and insurance.
A secondary impact on inventory is related to regulatory lag. Inventory balances are typically included in the original rate base during rate case filings. Unfortunately, as inventory balances grow, that growth often isn’t reflected in the current rates. The utility suffers a lag or delay in being able to recover these costs (if ever) in their rates.
These two impacts on inventory costs help make the case for inventory optimization and using inventory analytics to your advantage.
The need for inventory optimization to manage unplanned costs
Perhaps the most worrisome costs are those that are unplanned and unforeseen. Many companies don’t adequately budget for annual obsolescence of aging inventory that’s no longer used and useful.
Once inventory is identified as obsolete, it must be segregated from inventory, with the book value written off to an operations and maintenance expense account. Most organizations assign obsolete inventory expenses directly to the business unit and asset base, and not at a corporate level. This practice may lead to disincentives on behalf of the business units to proactively assess their aging inventory.
Many companies do not adequately budget for annual obsolescence of aging inventory that is no longer used and useful.
Five levers of inventory management
There are five inventory management methods that all have unique impacts—companies can use one or multiple methods.
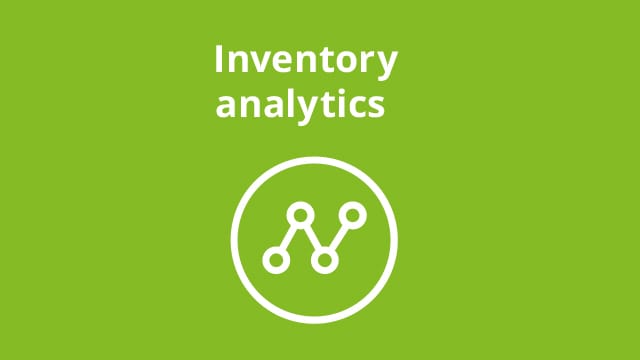
The logical question most companies have is, “How much inventory should I own?” Benchmarking inventory value with peer utilities is a good place to start. A common benchmark involves measuring the inventory value of maintenance and services (M&S) materials over megawatt-hours of generation.
A company’s stocking policies dictate how much inventory is stocked and where the inventory is held. Inventory stocking levels should also consider demand for the item over its lead time, which for high-volume items may be less than a few days. Utilities should ask themselves why they carry a high inventory stocking level if their suppliers are already stocking it.
Advanced analytics can be an important capability for improving inventory optimization. Leveraging predictive inventory consumption models can enable the assessment of expected inventory usage and stocking policies. With the help of inventory optimization analytics, utilities can determine what inventory is potentially needed and then conduct a deep dive into how and where to make improvements.
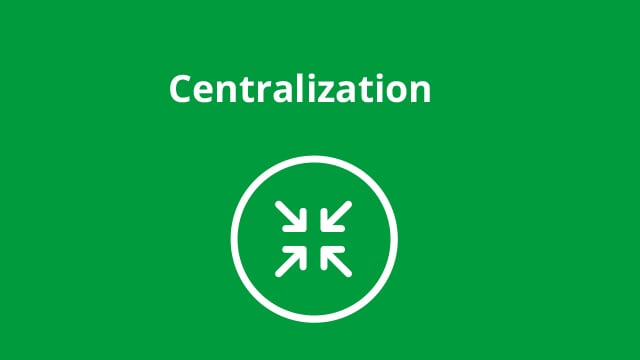
Establishing central inventory stocking policies for common materials that are used across several locations can lead to improved optimization and lower inventory investment. Companies should consider establishing virtual, pooled inventory policies at an enterprise or regional level instead of having individual stocking locations.
Most work management and inventory management systems have the capability to plan and manage inventory on an enterprise basis across multiple stocking locations. This can provide significant benefits in enabling distribution network optimization for stocking materials at a virtual or central location.
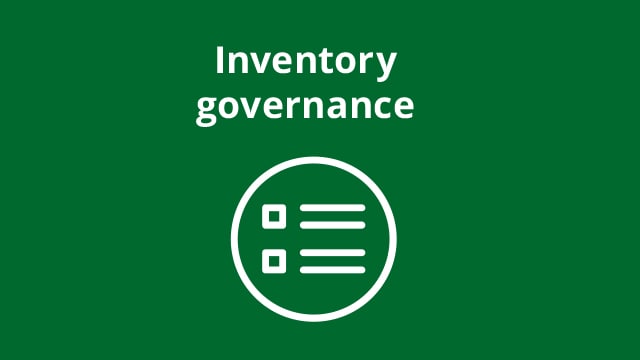
While governance is often overlooked, it could be one of the main drivers for improving inventory usage. Companies should consider establishing policies and guidelines for how they control inventory.
A leading practice is to establish a centrally managed team of experienced inventory professionals to be responsible for inventory governance. These professionals can evaluate requests to add items to inventory and to adjust inventory stocking levels. Additionally, a centralized team is often better positioned than local teams to make decisions related to accepting direct charge materials or returns into inventory. These decisions should be made on an analytical basis, free from local influence and bias.
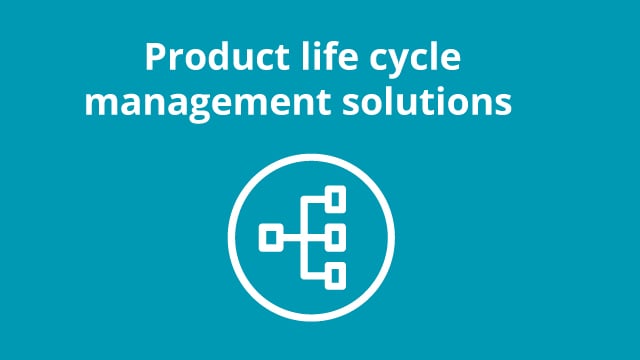
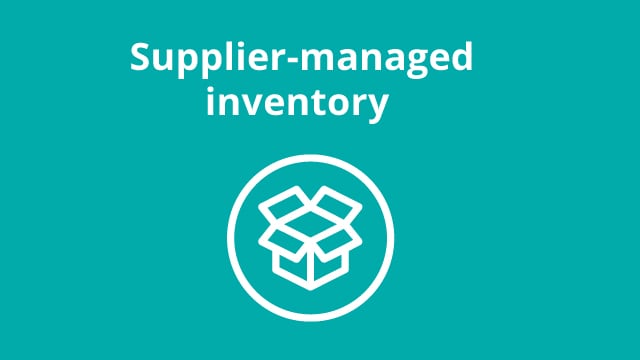
What inventory management method is right for you?
Adopting a holistic view of inventory management, combined with the use of marketplace tools, can help utilities control their inventory growth and improve inventory utilization. Deloitte has engaged with numerous clients across industries to help companies pull one or more of the five levers of inventory management.
Recommendations
Digital supply chain in retail and consumer goods
Using digital supply networks to gain competitive advantage
Why urban fulfillment centers?
How retailers are adapting to connected consumers