Entering the era of software-defined manufacturing has been saved
Perspectives
Entering the era of software-defined manufacturing
A new vision for smart manufacturing systems
Manufacturers face rising complexity—shorter product lifecycles, evolving consumer demands, and technology debt. To stay ahead, companies need software-defined manufacturing (SDM), a paradigm shift that unifies data, automation and workers to optimize smart factory systems. Learn how SDM is redefining the future of manufacturing and industry 5.0.
The power of software-defined manufacturing
Today, product designs often have a shorter shelf life. Changing consumer tastes require flexibility in production. Manufacturing contends with thousands of variations as attributes adjust over the product life cycle. Software content is increasing in many products, with software-enabled features updated during the manufacturing process. Meanwhile, enterprises are struggling to manage decades of technology debt, process debt, and resistance to change—all which hinder the agility needed in smart manufacturing.
To manage these challenges while also driving transformational change demanded by industry 5.0, a new vision is necessary—software-defined manufacturing (SDM). In this vision, data, software, automation, products, and human workers are aligned to close the gaps in smart manufacturing systems. Manufacturing operations are controlled, managed, and optimized using software applications and services. At its fullest potential, SDM is the seamless orchestration of people and machines across software-defined factories, networks, and supply chains.
Unpacking the paradigm shift and value unlocked by SDM
SDM’s impact lies in how it enables manufacturers to take new approaches to tackling problems, accessing knowledge, and orchestrating people and machines. SDM can improve operations at every step of the product life cycle, from capacity to product quality to worker experience, and ultimately drive financial impact.

${column1-large-text}
Modern scientific approach
SDM enables an evolved approach to operational excellence and new product development. SDM also allows for simulation-enhanced research and development, resulting in accelerated materials and pharmaceutical development. Organizations can leverage data science, AI, and connected software to fuel new solutions for familiar problems, often resulting in better outcomes than a traditional first principles approach.

${column2-large-text}
Knowledge access
SDM connects the factory ecosystem to manage and codify knowledge, eliminate information gaps, and facilitate access to knowledge. In this, knowledge access can become intuitive without specialized training or laborious work instructions. It also impacts how manufacturers connect employees and machines for greater collaboration and automation.

${column3-large-text}
Orchestration
With SDM, manufacturers can access a new level of connectivity, collaboration, and human-machine orchestration to optimize processes and outcomes. This integration extends from the shop floor to the C-suite, factory to factory, and across external partner networks.
${column4-large-text}
${column4-title}
The challenge of change
Externally, manufacturers face mounting cost pressures and customer demands, with rising expectations for higher product quality, greater personalization, and lower costs. Internally, workforce constraints remain a challenge, with over 80% of manufacturers citing them as a reason for turning down business.1
Meanwhile, legacy technologies on the factory floor lag behind innovation, limiting flexibility and agility across engineering and manufacturing. Even when systems are updated, the impact is often confined to a single factory rather than the entire network.
Determining the necessary enterprise changes to access software-defined manufacturing presents a challenge. Several key factors require attention:
- Siloed data and technologies inhibit connectivity and orchestration.
- Information technology (IT) and operational technology (OT) systems may be disparate and unintegrated.
- Cybersecurity risks become even more business critical as increasing data flows, devices, cloud services, and enabling hardware create attack vectors and vulnerabilities.
- Technology adoption both complicates and enables software/hardware abstraction.
A holistic approach is needed to align business strategy, technology investment, design and governance, and talent considerations. The goal is full ecosystem connectivity in a software-defined factory, where SDM environments, products, and interfaces provide visibility and traceability across engineering and smart manufacturing systems.
The impact of maturing and emerging technologies
Software-defined manufacturing is enabled by a range of technologies. These technologies are typically standard in IT environments, but they tend to be rarer in OT. Meanwhile, bleeding-edge innovation marches forward, and SDM is also enabled by new technologies that are only just emerging.
Taking the next steps toward SDM
SDM may take different shapes depending on the manufacturing sector and the nature of its production.
Investing in structured, integrated, and efficient frameworks accelerates digital transformation at scale to achieve strategic goals. Architecture and infrastructure, designed thoughtfully with an eye on process orchestration, empower users to build and leverage a broad set of high-value use cases, at scale, with a modern workforce.
In determining where to start and what comes next, smart manufacturers encounter key questions in the areas of data management, governance, and the workforce experience.
Data management considerations
How do we prepare data for AI and scalable solutions?
How do we analyze the data?
How do we deliver insights to people—or systems—at the right time?
Technology governance considerations
How do we do this securely?
How do we apply this at different levels of scale across operations?
How do we transform the software development life cycle?
Workforce considerations
How does SDM enhance the workforce experience?
How do we roll out and sustain new ways of working?
Real-world examples of SDM
See how two organizations applied software-defined manufacturing to manage a rapid increase in shipment volume with limited maintenance windows and enhance workplace safety while expanding capacity across their network.

Enabling predictive maintenance from the edge
A global transportation client experienced an increase in shipment volume, spurring 24/7 operations which limited maintenance windows. The organization needed a predictive maintenance strategy to reduce capacity loss, drive efficiencies, and optimize delivery service levels.
To help the client scale outcomes, connect its disparate systems, and merge that data at the edge before sending to the cloud, we recognized the importance of adopting a modern architecture strategy and recommended the client adopt a unified namespace to facilitate its operational data management needs.

Building the plant of the future
A large industrials company faced growing demand to create more capacity across its network while enhancing safety. The company focused on eight areas and 25 improvement targets, including expanding capacity, improving safety, and increasing product quality. To address these priorities, the organization adopted key technologies to fuel three value-driving solutions:
- Enhancing workplace safety with AI.
- Improving cycle time with predictive maintenance.
- Reducing unplanned downtime with real-time sensors.
Taking the next steps on the path to SDM
There are two overarching aspects to software-defined manufacturing transformation. First, a continued focus on engineering principles to create flexible products that adapt over time to customer demands and new technology.
Second, a recognition that automation and factory tooling require high up-front costs for hardware, but that as SDM’s efficiency and productivity gains take effect, these initial costs give way to savings and revenue.
SDM requires executive sponsorship and change leaders across functions. By aligning decisions and investments with enterprise strategy, executives can drive change and engage organization-wide stakeholders to leverage smart manufacturing.
Technology innovation is moving fast. Modernize opportunistically with investments in foundational capabilities and process transformation. Take a holistic view of technologies that drive incremental, high-frequency use cases with lower costs and effort. Design for connected data and integrated systems within software-defined factories, across the network, and throughout the supply chain.
Finally, leaders should approach SDM with the human workforce in mind as they move towards the future of manufacturing. New technologies require new skills but should build on existing knowledge.

Embrace the future of manufacturing
In our full report, “Entering the era of software-defined manufacturing: A vision for productivity,” we share real-world case studies of SDM in practice, in-depth analysis of this new vision for smart manufacturing, and actionable insights to stay competitive in the industry 4.0 landscape.
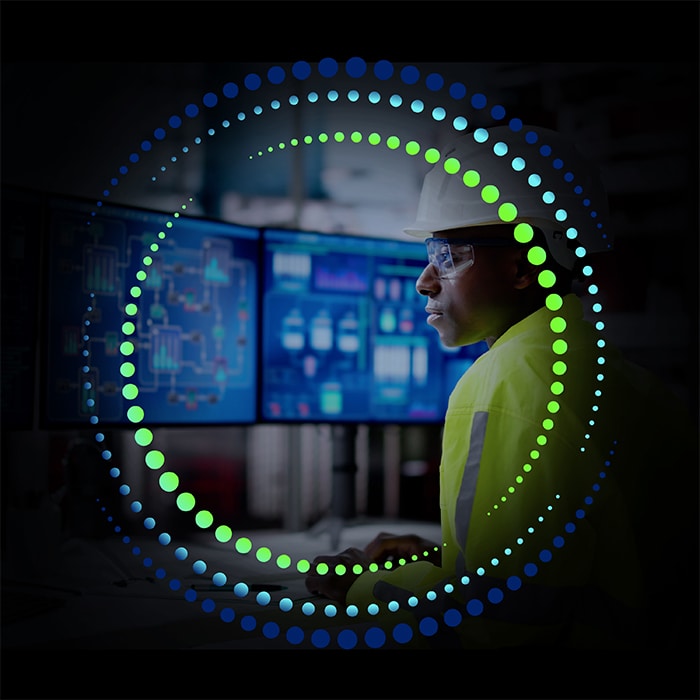
It’s time to operate on all cylinders
Ready to unleash the potential of smart operations? Revolutionize your production processes, enhance performance, and accelerate growth with Deloitte’s IndustryAdvantage™ approach to operations transformation.
Get in touch

Industrial Products and Construction Leader
Principal, Deloitte Consulting LLP

Smart Manufacturing
Specialist Leader, Deloitte Consulting LLP
Acknowledgments
The authors would like to thank subject-matter specialists
Jason Bergstrom; Lindsey Berckman; Stavros Stefanis; Rohini Prasad; Alex
Bredemus; Leslie Koff; Chris Culver; Chris Como; Jon Tidd and Zachary Drew of
Deloitte Consulting LLP, and Jason Hunt and Anne Robbins of Deloitte & Touche
LLP who played an instrumental role in the development and publication of this
business paper. Your invaluable insights and contributions have significantly
enriched the quality and depth of this work.
End notes
1Deloitte & The Manufacturing Institute Perception Study, 2021
2“What Are Industry Cloud Platforms?,” Gartner.com, November 16, 2023.
Recommendations
Smart manufacturing solutions
Discover Deloitte's Smart Manufacturing solutions for factory automation, industrial IoT solutions, and reaching sustainable manufacturing goals.
Industrial DataOps and Unified Namespace
Reshaping modern manufacturing and enabling AI